Are you looking cost of goods manufactured schedule? This article will share some tips and tricks to help you. We’ve got you covered from finding ways to reduce your cost of goods manufactured schedule, negotiating better deals, and automating your processes. So, go ahead and take advantage of our tips, and start saving on your manufacturing costs today!
What is the cost of goods manufactured schedule?
The cost of goods manufactured schedule is a guide that helps businesses save on their manufacturing costs. The schedule can be used to identify where costs are high and where they could be lowered to improve business operations. By creating a schedule, you can ensure that your manufacturing process runs smoothly and with minimal cost.
What are the benefits of using the cost of goods manufactured schedule?
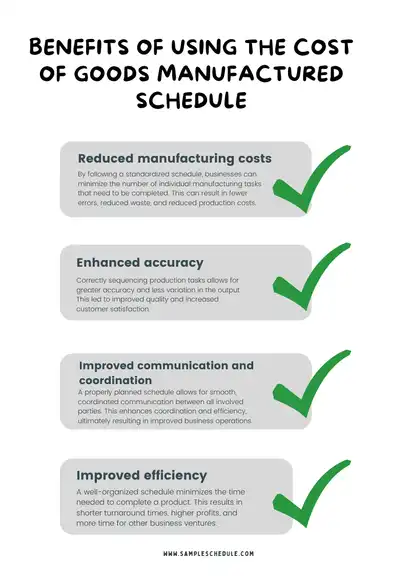
benefits of using the cost of goods manufactured schedule
When following the cost of goods manufactured schedule, businesses can optimize their production processes and achieve significant cost savings. Below are some of the benefits that can be realized when using this method:
- Reduced manufacturing costs: By following a standardized schedule, businesses can minimize the number of individual manufacturing tasks that need to be completed. This can result in fewer errors, reduced waste, and reduced production costs.
- Enhanced accuracy: Correctly sequencing production tasks allows for greater accuracy and less variation in the output. This led to improved quality and increased customer satisfaction.
- Improved communication and coordination: A properly planned schedule allows for smooth, coordinated communication between all involved parties. This enhances coordination and efficiency, ultimately resulting in improved business operations.
- Improved efficiency: A well-organized schedule minimizes the time needed to complete a product. This results in shorter turnaround times, higher profits, and more time for other business ventures.
Following a schedule of cost of goods manufactured is beneficial for any business, regardless of size or industry. These tips can ensure success and reduce your overall manufacturing costs.
Why is the cost of goods manufactured schedule important?
The cost of goods manufactured schedule is important for ensuring accurate and timely financial information. The schedule helps optimize business operations by providing a detailed picture of how much inventory is available, how much money has been spent, and how much is left in the budget. It also identifies which products are selling well and which may be over-producing. The schedule can also help improve the quality and profitability of a business’s manufacturing operations.
Making the cost of goods manufactured schedule a regular part of business operations can be challenging, but it is well worth the investment. There are many factors to consider when creating the schedule, including but not limited to production goals, customer demand, and manufacturing constraints. Consult with an experienced consultant to start creating your schedule of the cost of goods manufactured.
How is the cost of goods manufactured schedule calculated?
A cost of goods manufactured schedule is a tool businesses can use to track and analyze their manufacturing costs. The schedule of cost of goods manufactured is based on various factors, including the volume and value of the products being manufactured.
The cost of goods manufactured schedule can help identify areas where costs might increase or decrease. By tracking the changes in these factors, businesses can make informed decisions about how to optimize their manufacturing processes. Additionally, businesses can create better plans by understanding where costs increase.
Another benefit of using the cost schedule of goods manufactured is that it can be used to create better data. By following specific steps, businesses can ensure accuracy and consistency in their data. This data can then be used to make informed decisions about future operations.
When creating the cost schedule of goods manufactured, it is important to consider various factors. By taking the time to create a proper schedule, businesses can save money on their manufacturing costs.
How can the schedule of cost of goods manufactured to be used to improve business operations?
The schedule of cost of goods manufactured is an important tool that businesses can use to optimize production and improve efficiency.
By understanding the costs associated with manufacturing, businesses can make informed decisions about allocating resources and improving profitability.
Additionally, businesses can manage inventory more accurately and reduce costs associated with overstock by using the schedule of goods manufactured.
Finally, by creating a schedule of cost of goods manufactured, businesses can better assess their competition and identify opportunities for improvement. Implementing a schedule of cost of goods manufactured is essential to becoming more financially successful.
Read Also: 30+ Free Employee Shift Schedule Template Excel
What are some common mistakes when creating the cost of goods manufactured?
One of the most common mistakes made when creating the schedule of cost of goods manufactured is failing to include labor on the schedule. This can lead to underpayment, exploitation, or even labor upheavals. Accurate forecasting can cause unexpected expenses, such as overtime pay or replacement parts.
Additionally, automating a process without verifying it saves time and money but can lead to waste. Poor planning can also lead to inaccurate calculations of costs and shortages. By following these tips, you can create a schedule of cost of goods manufactured that is accurate and efficient, helping your business save money and improve operations.
Conclusion
When creating the cost of goods manufactured schedule, businesses should be sure to take into account a variety of factors. Doing so can ensure accuracy and consistency in production and get the most value for their money. However, businesses make a few common mistakes when creating this schedule. Businesses can avoid these mistakes and save on manufacturing costs by understanding them.